數(shù)字隔離器在工業(yè)電機驅動應用中的優(yōu)勢
工業(yè)電機驅動中使用的電子控制必須能在惡劣的電氣環(huán)境中提供較高的系統(tǒng)性能。電源電路會在電機繞組上導致電壓沿激增現(xiàn)象,而這些電壓沿則可以電容耦合進低電壓電路之中。電源電路中,電源開關和寄生元件的非理想行為也會產(chǎn)生感性耦合噪聲。控制電路與電機和傳感器之間的長電纜形成多種路徑,可將噪聲耦合到控制反饋信號中。高性能驅動器需要必須與高噪聲電源電路隔離開的高保真反饋控制和信號。在典型的驅動系統(tǒng)中,包括隔離柵極驅動信號,以便將逆變器、電流和位置反饋信號驅動到電機控制器,以及隔離各子系統(tǒng)之間的通信信號。實現(xiàn)信號隔離時,不得犧牲信號路徑的帶寬,也不得顯著增加系統(tǒng)成本。光耦合器是跨越隔離柵實現(xiàn)安全隔離的傳統(tǒng)方法。盡管光耦合器已使用數(shù)十年,其不足也會影響系統(tǒng)級性能。
變速電機驅動器在工業(yè)應用中的廣泛使用要歸功于高效電源開關和具有成本優(yōu)勢的電子控制電路。設計上的困難則是用低壓控制電路耦合高功率開關電路,而不犧牲抗噪性能或開關速度。
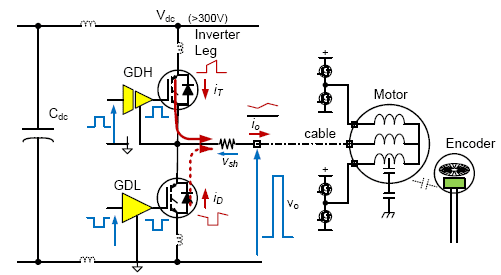
圖1. 包括寄生元件的逆變器電路。
現(xiàn)代開關逆變器的效率一般超過95%,所用功率晶體管開關還可連接高壓直流軌高軌與低軌之間的電機繞組。這一過程可以減少逆變器的損耗,因為功率晶體管工作于完全飽和模式下,而該模式會降低傳導時的壓降和功率損耗。開關過程中還存在額外的功率晶體管損耗,因為在此期間,晶體管上有一較大的電壓,與此同時,負載電流在高、低功率設備之間進行切換。功率半導體公司設計出IGBT之類開關時間較短的晶體管,以減少這種開關功率損耗。然而,這種較高的開關速度也會帶來一些無用的副作用,比如開關噪聲增加。
在驅動器控制端,VLSI工藝的持續(xù)進步改善了混合信號控制電路的成本和性能,為高級數(shù)字控制算法的廣泛應用以及交流電機效率的提高創(chuàng)造了條件。提升性能付出的代價是IC工作電壓從12 V至5 V降低至現(xiàn)在的3.3 V,結果提高了對噪聲的靈敏度。這種傳統(tǒng)的噪聲過濾方法通常不太適用,因為往往需要維持驅動系統(tǒng)的帶寬,而帶寬一般都是一個關鍵的性能參數(shù)。
電機驅動逆變器環(huán)境
三相逆變器是一種功率電子開關電路,控制功率從直流供電軌到三個交流電機繞組的流動。逆變器有三條相同的腿,每條腿包括兩個IGBT晶體管和兩個二極管,如圖1所示。每個電機繞組均連接至通過分流器連接高端晶體管和低端晶體管的同一節(jié)點。逆變器使電機繞組在直流總線的高壓軌和低壓軌之間切換,以控制平均電壓。繞組具有極高的電感性,將阻擋電流的變化,因此,當功率晶體管關閉時,電流將開始在連接至相反電源軌的二極管中流動。這樣,即使逆變器功率設備和直流鏈路電容中存在斷續(xù)傳導,也會有電流連續(xù)流到電機繞組中。電機繞組阻抗充當來自逆變器的高壓脈沖寬度調制方波輸出電壓的低通濾波器。
將低壓控制電流連接至逆變器時存在巨大的困難。一個基本問題是,高端晶體管發(fā)射器節(jié)點在高壓總線高供電軌與低供電軌之間切換。首先,高端驅動器必須能夠驅動相對于一個發(fā)射器(可能比共用輸入信號高300 V或以上)的柵極信號。其次,通過分流器(vsh)的電機電流信號必須從300 V或以上的共模電壓中提取出來。其他問題將由電源電路中的寄生元件導致。當功率晶體管或二極管的開關頻率超過1 A/ns時,即使是10 nH的PCB走線電感也可能導致顯著的電壓(>10 V)。寄生電感和部件電感會導致振鈴,結果使設備開關產(chǎn)生的噪聲脈沖的持續(xù)時間變長。甚至電機電纜的高頻阻抗也可能帶來問題,因為出于安全考慮,配電板可能離電機很遠。其他效應包括噪聲從電機耦合到反饋傳感器信號中,其原因是快速切換的繞組電壓波形。問題將變得更加嚴重,因為驅動電路的功率額定值將增加電路板的物理尺寸,結果將進一步增加寄生電感,甚至提高電流和電壓開關速率。通過隔離控制和電源電路消除噪聲耦合現(xiàn)象,是應對這一問題的主要工具之一。隔離電路的性能是決定驅動性能的一個關鍵因素。在轉軸轉動時,轉軸位置編碼器將產(chǎn)生頻率為100 kHz或以上的數(shù)字脈沖流。然而,在許多情況下,編碼器上安裝的電路會提高設備的精度,并使數(shù)據(jù)速率增加到10 Mbps以上。另外,跨越分流器的反饋信號也可以隔離,方法是先把數(shù)據(jù)轉換成數(shù)字位流,然后把該位流與低功耗電路隔離開來。這種情況下,數(shù)據(jù)速率為10 Mbps至20 Mbps。
柵極驅動電路所需要的開關性能似乎并不高,因為電機驅動逆變器的開關速率很少超過20 kHz。然而,需要在高端設備和低端設備的開關信號之間插入一個死區(qū),以防止發(fā)生直通。死區(qū)為功率開關的開啟和關閉延遲以及隔離電路所致延遲的不確定性的函數(shù)。死區(qū)延長會給逆變器傳遞函數(shù)帶來更多非線性,結果將產(chǎn)生無用的電流諧波,并可能降低驅動效率。
因此,跨越電源電路和控制電路之間的隔離柵發(fā)送數(shù)據(jù)的方法不得在開關過程中帶來時序的不確定性,并須具備較強的抗噪能力。
評論